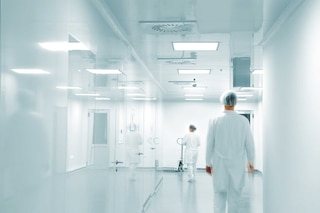
Cleanroom: het uitsluiten van contaminatie
Cleanrooms zijn ontworpen om de farmaceutische, voedsel- en chemische industrie in staat te stellen in de lucht aanwezige micro-organismes, fijn stof of chemische dampen te beperken en zo te voorkomen dat deze producten contamineren. Deze contaminatie kan de kwaliteit van de goederen aantasten en besmettingen veroorzaken, met ernstige gezondheids-, of economische risico's en kan de reputatie van het bedrijf ernstig schaden.
Daarom moeten ondernemingen in bepaalde sectoren beschikken over cleanrooms. Dit zijn ruimten die speciaal zijn ontworpen voor bijzondere omgevingscondities en om een besmettingsniveau van nul te handhaven. Hiertoe moeten de normen voor het ontwerp, de bouw en het gebruik van deze ruimten in acht worden genomen. Tegelijkertijd is het van belang de reiniging en ontsmetting zeer zorgvuldig en op dagelijkse basis uit te voeren.
In dit artikel wordt gedefinieerd wat cleanrooms zijn, hoe ze worden ontworpen en gerealiseerd, alsmede de toepassing ervan in een warehouse.
Definitie van een cleanroom
Een cleanroom is een zeer zuivere, schone en gesteriliseerde werkomgeving, waar de luchtstromen, de luchtdruk, de temperatuur, de vochtigheidsgraad en het lichtniveau strikt worden gecontroleerd, binnen de grenzen die door de geldende regelgeving zijn kracht zijn. Diverse processen en bewerkingen kunnen hier veilig en zonder enige vorm van contaminatie worden uitgevoerd.
Deze voorzieningen zullen specifiek moeten worden ontworpen, en moeten uitgerust worden met de noodzakelijke middelen, zoals bijvoorbeeld HEPA-filters, luchtdouches en luchtsluizen. Alleen bevoegd personeel heeft toegang tot de cleanroom voor het uitvoeren van de benodige taken, zonder de goederen bloot te stellen aan ziektekiemen die ze zouden kunnen contamineren.
Het gebruik van cleanrooms
Het cleanroom-concept vindt zijn oorsprong in operatiekamers van ziekenhuizen. Het is logisch dat chirurgische ingrepen, een goede ventilatie van de operatiekamer, de sterilisatie van het gereedschap en strikte hygiënische normen vereisen.
Vervolgens werden cleanrooms in de industrie ingevoerd, met als doel contaminaties onder controle te houden, hetgeen van fundamenteel belang is voor de veiligheid van de producten die er worden vervaardigd. Sindsdien heeft het gebruik ervan zich uitgebreid tot tal van sectoren: de voedingsmiddelenindustrie, de gezondheidszorg en de technologische sector.
De aanwezigheid van micro-organismen in de lucht kan de eigenschappen van bepaalde producten wijzigen. In het geval van levensmiddelen, zoals bij vlees, vis, zuivelproducten, groenten en fruit of kant-en-klaarmaaltijden, kan de aanwezigheid daarvan een aanzienlijk gezondheidsrisico inhouden, met vergiftiging en infecties tot gevolg.
Cleanroom voorschriften
Het beheersen en beperken van contaminaties in een cleanroom is geen gemakkelijke taak, en vereist een zeer nauwkeurig ontwerp van de ruimte. Een groot aantal elementen moet worden gerespecteerd: van de technische kenmerken die nuttig zijn voor de goede werking, zoals de HEPA-filters die onmisbaar zijn, de constructienormen en de adequate uitrustingen, tot de doorstroming van de medewerkers en de goederen.
Bij het ontwerpen en de constructie, moet rekening worden gehouden met twee normen waarvan de criteria, de kenmerken van een cleanroom bepalen:
- De GMP, of de goede manier van produceren: Good Manufacturing Practices. Dit is een internationale verordening betreffende de vervaardiging van geneesmiddelen, cosmetica of voedingsmiddelen, onder optimale omstandigheden. In Europa wordt dit geregeld door Verordening 1223/2009 van het Europees Parlement en de Raad van 30 november 2009 betreffende cosmetische producten. Dit betekent dat er niet alleen voor schone lucht in de cleanroom moet worden gezorgd, maar ook voor een goede algemene temperatuurbeheersing, passende verlichting en brandbeveiliging. Het is ook van essentieel belang, dat in de ruimte waar de werkzaamheden worden uitgevoerd, gesteriliseerde producten en aseptische oppervlakken worden gebruikt.
- De norm ISO 14644. Dit is een internationale norm, die door de International Organization for Standardization (ISO) - Internationale Organisatie voor Normalisatie - is vastgesteld, om de zuiverheid van de lucht in cleanrooms te garanderen. Deze norm classificeert werkruimten in negen categorieën, en stelt uiterste grenswaarden vast, voor zwevende deeltjes in gesloten ruimtes. Deze classificatie is min of meer restrictief, afhankelijk van het soort industrie. Van slechts 0,2 micrometer deeltjes per kubieke meter lucht (luchtvaart-, farmaceutische en ziekenhuissector) tot 293.000 micrometer. Het hoofddoel van de bouw van een cleanroom is het beperken en het vasthouden van vervuilende deeltjes. En het voorkomen dat deze verontreinigende deeltjes in de ruimte terechtkomen.
Een cleanroom ontwerpen en realiseren
Bij het ontwerpen van een cleanroom gaat het erom te beslissen hoe de ruimte moet worden ingedeeld, hoe veiligheidshekwerken, deuren, ramen, filters en toegangen moeten worden geïnstalleerd, en hoe de vloer moet worden aangelegd. Bij het ontwerpen, moet rekening worden gehouden met de functie van de cleanroom en met de externe omstandigheden.
De materialen die voor de bouw van cleanrooms worden gebruikt, moeten van een hogere kwaliteit zijn, dan die welke in andere soorten constructies worden gebruikt. Aan bepaalde voorwaarden moet worden voldaan: duurzaamheid, bestendigheid tegen chemische stoffen, eenvoudig te reinigen en brandwerendheid.
De norm ISO 14644 stelt bepaalde eisen aan de structuur van de cleanroom:
- Veiligheidshekwerken en plafonds. Deze moeten worden gemaakt van sandwichpanelen, d.w.z. van panelen van innovatief bouwmateriaal uit één stuk, bestaande uit een laag isolatiemateriaal tussen twee platen geprofileerd plaatmateriaal, dat voor stevigheid zorgt en het paneel andere eigenschappen geeft, zoals een goede brandwerendheid en thermische isolatie. De montage van de verschillende panelen moet nauwkeurig gebeuren om besmetting door micro-organismen en ophoping van stof te voorkomen en het schoonhouden te vergemakkelijken.
- Deuren en ramen. Deuren moeten ook gemaakt zijn van sandwichpanelen en ramen moeten voorzien zijn van dubbele beglazing voor de veiligheid.
- Vloeren. Ze kunnen verschillende afwerkingen hebben, afhankelijk van de verplaatsingen in de ruimte. Bij voorkeur moeten deze glad zijn om stofophoping te voorkomen. Ook moeten ze gemakkelijk schoon te maken zijn en bestand zijn tegen aantasting door mico-organismen.
- Verlichting. Het gebruik van TL-verlichting met neutraal wit licht is vereist.
De volgende stap in het ontwerpen van de ruimte is de analyse van de luchtfiltering, één van de belangrijkste criteria voor een cleanroom. De lucht die deze afgesloten ruimte binnenkomt, wordt gefilterd om zwevende deeltjes te verwijderen en meerdere malen per dag vernieuwd om stofvorming te voorkomen. Daarom worden HEPA-filters, die van glasvezels zijn gemaakt, gebruikt om micro-organismen tegen te houden.
Ook moeten cleanrooms van airconditioning worden voorzien om het productieproces soepel te laten verlopen, goede werkomstandigheden voor de werknemers te creëren en het risico op kruisbesmetting tot een minimum te beperken.
Tenslotte wordt ten zeerste aanbevolen een SAS (Security Airlock System) of luchtsluis te installeren, een doorgang tussen twee ruimten waarvan de lucht niet of zo min mogelijk gemengd mag raken, met twee snelloopdeuren, één naar de cleanroom en één naar buiten, zodanig dat deze nooit tegelijk geopend worden. Dankzij dit systeem worden plotselinge veranderingen in temperatuur en luchtdruk vermeden, telkens wanneer u de cleanroom binnengaat.
-
Een SAS of luchtsluis bevat twee snelloopdeuren die nooit tegelijk worden geopend om plotselinge veranderingen in temperatuur of luchtdruk te voorkomen Het belang van het schoonmaken van een cleanroom
Zodra de bouw- en ontwerpfase van de cleanroom is afgerond, is ook het onderhoud ervan belangrijk. Het schoonmaken van een cleanroom is een fundamentele vereiste. Het is belangrijk om de hygiëne van de medewerkers te controleren, en na te gaan of het materiaal gedesinfecteerd en schoon is. Daarom moeten werknemers goed worden opgeleid en bewust worden gemaakt van het belang van dit onderwerp. Ze moeten speciaal ontworpen werkkleding dragen om de verontreinigende stoffen die de huid en het lichaam op natuurlijke wijze produceren, op te vangen, en in sommige gevallen moeten er haarnetjes, handschoenen en maskers worden gebruikt.
Toegang is één van de belangrijkste aandachtspunten in cleanrooms, aangezien hier het grootste risico op het binnendringen van zwevende deeltjes aanwezig is. Om dit risico tot een minimum te beperken, worden er luchtdouches voor de medewerkers geïnstalleerd. Dit zijn afgesloten ruimten waar bacteriën van mensen worden verwijderd voordat ze de cleanroom ingaan.
Cleanrooms in het magazijn
Transportbanden van roestvrij staal zijn zeer goed bestand tegen corrosie In de logistiek heeft het cleanroom-concept een duidelijke toepassing: vries- en koelruimten. Dit zijn geïsoleerde ruimtes om warmteoverdracht te voorkomen. Koeling is één van de meest gebruikte methoden om producten, vooral levensmiddelen of geneesmiddelen, gedurende een bepaalde tijd te conserveren.
Om ervoor te zorgen dat een kamer thermisch geïsoleerd is, moeten muren, plafonds, vloeren en deuren gemaakt zijn van materialen die de overdracht van warmte tegengaan. Ook moeten er compressoren en verdampers worden geïnstalleerd op het bovenste gedeelte van het gebouw. Het hoofddoel is een stabiele temperatuur te handhaven gedurende het gehele logistieke proces, en kritische elementen te elimineren, aangezien deze de koudeketen van de producten zouden kunnen doorbreken.
Het is gebruikelijk om hoge, zelfdragende ruimtes te creëren, die werken bij een constante temperatuur. Deze gebouwen hebben een structuur die bestaat uit metalen magazijnstellingen waaraan de sandwichpanelen, verticale veiligheidshekwerken en de overkapping zijn bevestigd. Dit type constructie neemt alleen die ruimte in, die nodig is voor een optimale opslagcapaciteit. Eén van de belangrijkste voordelen is de verlaging van de energiekosten, die voortvloeien uit het feit dat het systeem op een lage constante temperatuur moet worden gehouden.
Cleanrooms en automatische magazijnen
In de logistiek waarbij een constante temperatuur gewaarborgd moet worden, wordt automatisering steeds belangrijker. Het is een oplossing die zowel een optimale opslagcapaciteit, als een totale beheersing van de omstandigheden ten aanzien van de afhandeling van de producten, mogelijk maakt. Transportbanden en magazijnkranen zorgen voor een continu en efficiënte verplaatsing van de goederen. Hierdoor worden de doorlooptijden verkort, hoeven er minder goederen handmatig te worden afgehandeld, en worden de daarmee gepaard gaande risico’s beperkt.
De meest gebruikte automatische opslag- en transportoplossingen in vries- en koelruimten:
- Industriële transportbanden. Deze vervangen de traditionele apparatuur voor goederenafhandeling en verplaatsen de producten automatisch. Transportbanden van roestvrij staal worden bijzonder aanbevolen voor dit type opslagruimte, omdat ze zeer goed bestand zijn tegen corrosie.
- Magazijnkranen. Een magazijnkraan verplaatst de goederen vanaf de voorkant van het gangpad, naar hun overeenkomstige opslaglocatie. De magazijnstellingen kunnen enkeldiep of dubbeldiep zijn.
- Het Pallet Shuttle-systeem. De werking is volledig automatisch, aangezien het gebruikt maakt van een gemotoriseerde shuttle, die de laadeenheden verplaatst. Het is één van de meest efficiënte opslagsystemen die er op de markt te krijgen zijn. Het gebruik ervan verhoogt de productiviteit, aangezien het een groter aantal in- en uitslagcycli mogelijk maakt.
- De implementatie van een warehouse management systeem (WMS), zoals Easy WMS van Mecalux, draagt bij aan de verhoging van de productiviteit van een automatisch magazijn. Het stuurt alle elementen aan, die met elkaar in verbinding staan in een logistieke faciliteit, van de apparatuur voor goederenafhandeling tot de activiteiten die bedoeld zijn om de producten efficiënt te beheren.
Controle, reiniging en veiligheid
Bedrijven op het gebied van de levensmiddelenindustrie, de farmaceutische industrie of de chemische industrie, zijn genoodzaakt zogenaamde cleanrooms te gebruiken, om producten veilig te kunnen produceren of te verwerken. Deze installaties zijn geïsoleerd om ervoor te zorgen dat de lucht wordt gefilterd en dat er geen contaminerende deeltjes in deze ruimten kunnen komen, zodat de kwaliteit van de goederen niet wordt aangetast of beïnvloed.
In de logistieke sector is een volledig geïsoleerde faciliteit een koel- of vriescel. Hier worden producten opgeslagen die op een constante temperatuur moeten worden gehouden. De thermische isolatie zorgt ervoor dat de kou binnen blijft.
Mecalux heeft vele jaren ervaring in het ontwikkelen van dit type magazijn, voor bedrijven in de voedingsmiddelen-, de chemische en de farmaceutische sector. Drie voorbeelden:
- Bem Brasil. Deze fabrikant van diepgevroren voorgebakken friet, heeft de vriescel (-30°C) uitgerust met een automatisch Pallet Shuttle-systeem met een opslagcapaciteit van meer dan 33.000 pallets. De onderneming heeft voor een systeem voor compacte opslag gekozen, omdat het geschikt is voor de opslag van massaconsumptieproducten met een groot volume aan pallets per artikelnummer.
- Schaal Chocolatier. Dit Franse bedrijf, leider in de productie van hoogwaardige chocolade, beschikt over een automatisch magazijn met vijf gangpaden voorzien van enkeldiepe magazijnstellingen, met een opslagcapaciteit van 6200 pallets. Vier gangpaden hebben een constante temperatuur van 14°C, en één gangpad heeft een temperatuur van 5°C. Eindproducten en halffabricaten, grondstoffen, verpakkingsmateriaal en benodigdheden voor de dagelijkse werkzaamheden worden in de magazijnstellingen geplaatst.
- Takeda. Het farmaceutische bedrijf Takeda heeft een automatisch hoogbouwmagazijn laten aanleggen, met een opslagcapaciteit van 6584 pallets. Het magazijn is uitgerust met een temperatuur- en vochtigheidscontrolesysteem, dat de temperatuur constant tussen 16 en 24°C houdt, en voorkomt dat de vochtigheidsgraad hoger wordt dan 70%.
Als u overweegt een cleanroom in uw magazijn in te richten, of een oplossing voor koude opslag zoekt, neem dan contact met ons op. Uw project zal bestudeerd worden, en wij zullen u de beste oplossing bieden.